Descripción general del conector de alto voltaje
Los conectores de alto voltaje, también conocidos como conectores de alta tensión, son un tipo de conector automotriz. Generalmente, se refieren a conectores con una tensión de operación superior a 60 V y se encargan principalmente de transmitir altas corrientes.
Los conectores de alto voltaje se utilizan principalmente en circuitos de alto voltaje y alta corriente de vehículos eléctricos. Funcionan con cables para transportar la energía del paquete de baterías a través de diferentes circuitos eléctricos hasta diversos componentes del sistema del vehículo, como paquetes de baterías, controladores de motor y convertidores DC/DC. Componentes de alto voltaje como convertidores y cargadores.
Actualmente, existen tres sistemas estándar principales para conectores de alta tensión: el conector estándar de baja tensión (LV), el conector estándar USCAR y el conector estándar japonés. De estos tres conectores, el de baja tensión (LV) es el de mayor difusión en el mercado nacional y cuenta con los estándares de proceso más completos.
Diagrama del proceso de ensamblaje del conector de alto voltaje
Estructura básica del conector de alto voltaje
Los conectores de alto voltaje se componen principalmente de cuatro estructuras básicas, a saber, contactores, aisladores, carcasas de plástico y accesorios.
(1) Contactos: partes centrales que completan las conexiones eléctricas, a saber, terminales macho y hembra, lengüetas, etc.;
(2) Aislante: sostiene los contactos y asegura el aislamiento entre los contactos, es decir, la carcasa interior de plástico;
(3) Carcasa de plástico: La carcasa del conector asegura la alineación del conector y protege todo el conector, es decir, la carcasa de plástico exterior;
(4) Accesorios: incluidos accesorios estructurales y accesorios de instalación, a saber, pasadores de posicionamiento, pasadores guía, anillos de conexión, anillos de sellado, palancas giratorias, estructuras de bloqueo, etc.
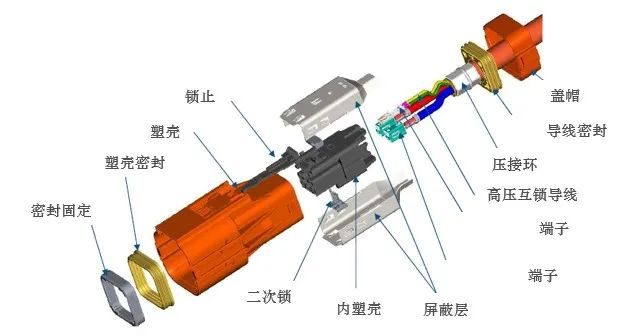
Vista ampliada del conector de alto voltaje
Clasificación de conectores de alta tensión
Los conectores de alta tensión se pueden distinguir de diversas maneras. Su clasificación se basa en si tienen función de blindaje, el número de pines, etc.
1.Si hay o no blindaje
Los conectores de alto voltaje se dividen en conectores sin blindaje y conectores blindados según tengan o no funciones de blindaje.
Los conectores sin blindaje tienen una estructura relativamente simple, carecen de función de blindaje y son relativamente económicos. Se utilizan en lugares que no requieren blindaje, como aparatos eléctricos cubiertos por carcasas metálicas, como circuitos de carga, interiores de baterías e interiores de controles.
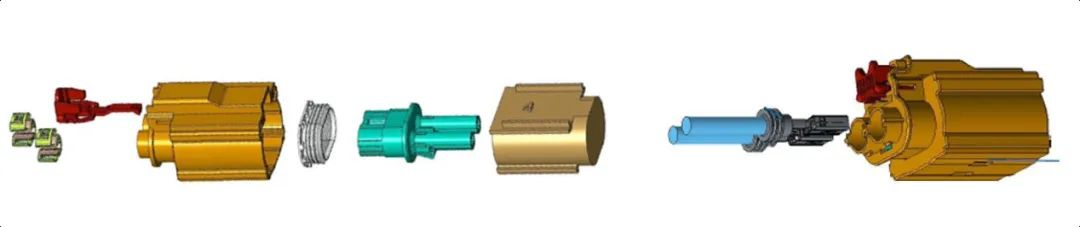
Ejemplos de conectores sin capa de blindaje y sin diseño de enclavamiento de alto voltaje
Los conectores blindados presentan estructuras complejas, requisitos de blindaje y costos relativamente altos. Son adecuados para lugares donde se requiere blindaje, como donde el exterior de aparatos eléctricos se conecta a arneses de cableado de alta tensión.
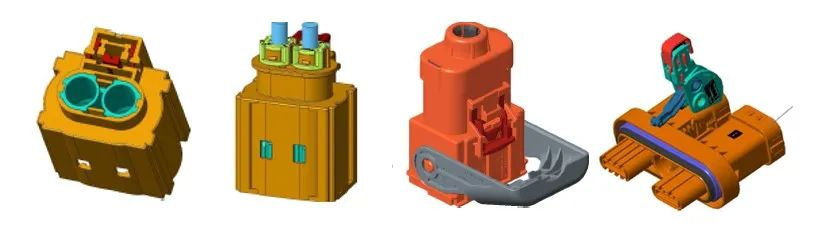
Conector con blindaje y diseño HVIL Ejemplo
2. Número de enchufes
Los conectores de alto voltaje se clasifican según el número de puertos de conexión (PIN). Actualmente, los más utilizados son el conector unipolar, el bipolar y el tripolar.
El conector 1P tiene una estructura relativamente simple y es económico. Cumple con los requisitos de blindaje e impermeabilización de los sistemas de alta tensión, pero el proceso de ensamblaje es algo complejo y su reutilización es deficiente. Se utiliza generalmente en baterías y motores.
Los conectores 2P y 3P presentan estructuras complejas y costos relativamente altos. Cumplen con los requisitos de blindaje e impermeabilidad de los sistemas de alta tensión y ofrecen buena facilidad de mantenimiento. Se utilizan generalmente para entrada y salida de CC, como en paquetes de baterías de alta tensión, terminales de controlador, terminales de salida de CC de cargadores, etc.
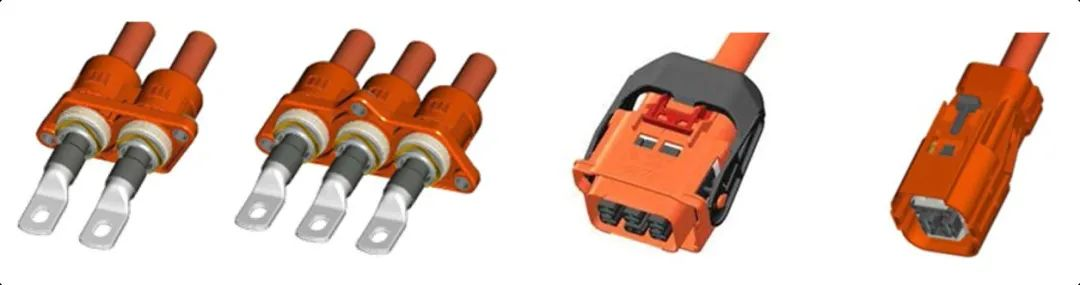
Ejemplo de conector de alto voltaje 1P/2P/3P
Requisitos generales para conectores de alta tensión
Los conectores de alto voltaje deben cumplir con los requisitos especificados por SAE J1742 y tener los siguientes requisitos técnicos:
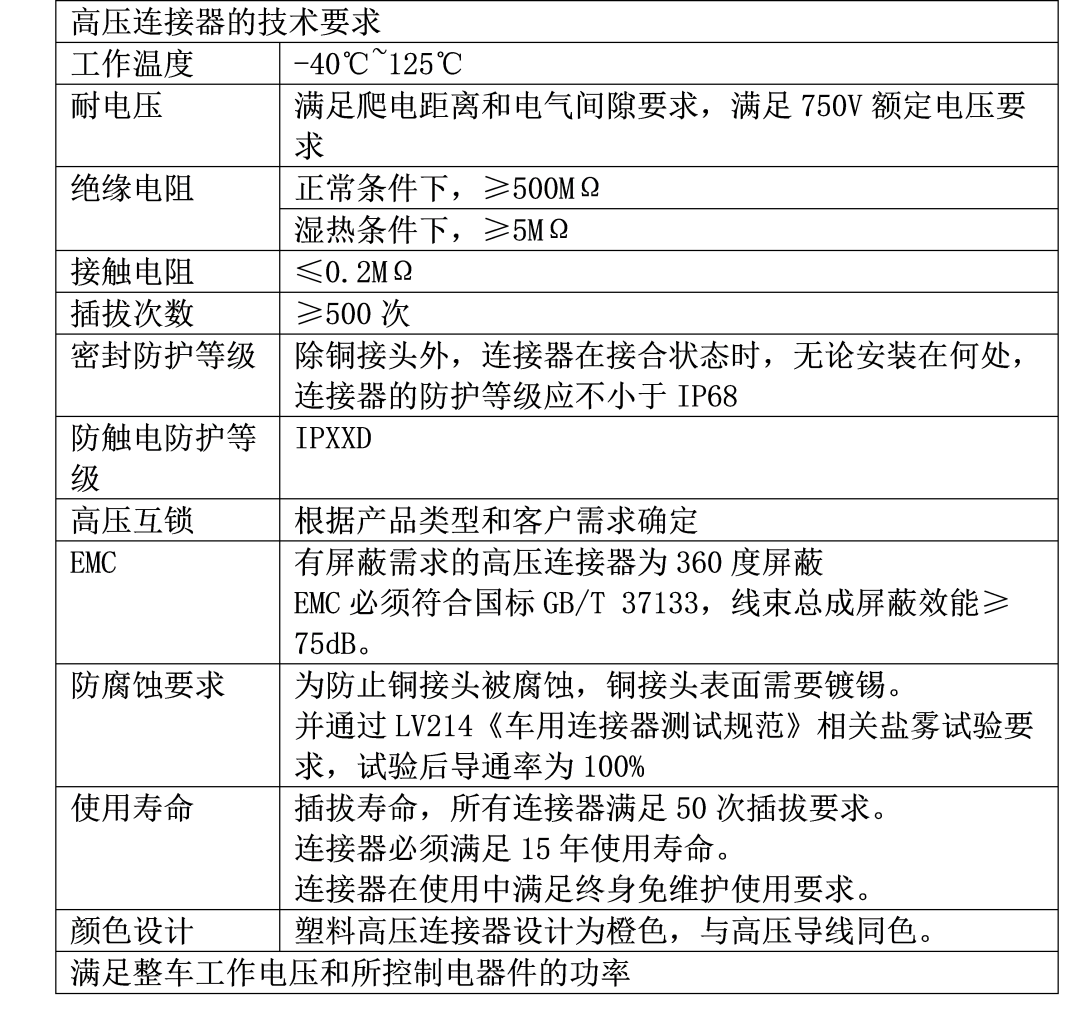
Requisitos técnicos especificados por SAE J1742
Elementos de diseño de conectores de alta tensión
Los requisitos para los conectores de alto voltaje en sistemas de alto voltaje incluyen, entre otros: alto voltaje y alto rendimiento de corriente; la necesidad de poder lograr mayores niveles de protección en diversas condiciones de trabajo (como alta temperatura, vibración, impacto de colisión, a prueba de polvo e agua, etc.); tener capacidad de instalación; tener un buen rendimiento de blindaje electromagnético; el costo debe ser lo más bajo posible y duradero.
De acuerdo con las características y requisitos anteriores que deben tener los conectores de alto voltaje, al comienzo del diseño de conectores de alto voltaje, se deben tener en cuenta los siguientes elementos de diseño y se deben realizar un diseño específico y una verificación de prueba.
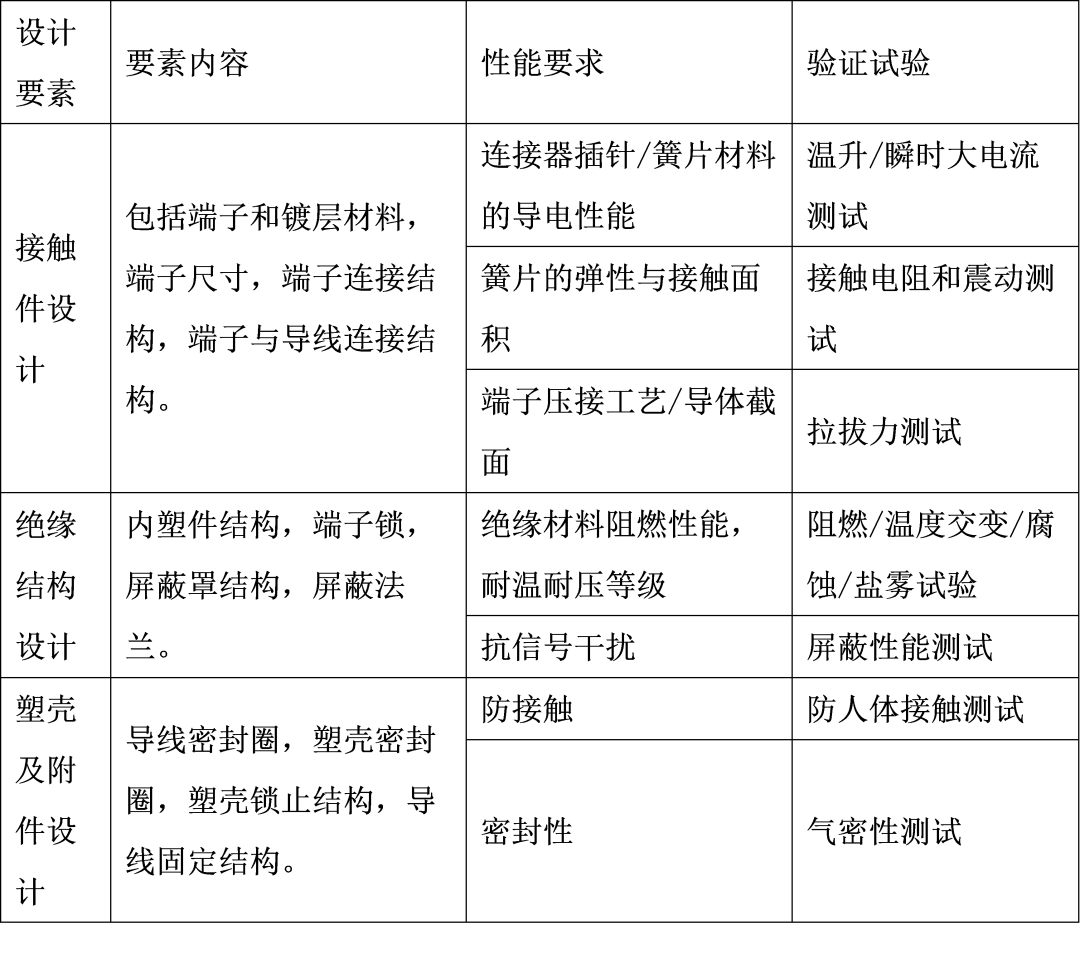
Lista comparativa de elementos de diseño, rendimiento correspondiente y pruebas de verificación de conectores de alta tensión
Análisis de fallos y medidas correspondientes de conectores de alta tensión
Para mejorar la confiabilidad del diseño del conector, primero se debe analizar su modo de falla para poder realizar el trabajo de diseño preventivo correspondiente.
Los conectores suelen tener tres modos de falla principales: mal contacto, mal aislamiento y fijación floja.
(1) En caso de mal contacto, se pueden utilizar indicadores como la resistencia de contacto estático, la resistencia de contacto dinámico, la fuerza de separación de un solo orificio, los puntos de conexión y la resistencia a la vibración de los componentes para evaluar;
(2) En caso de mal aislamiento, se pueden detectar la resistencia de aislamiento del aislador, la tasa de degradación temporal del aislador, los indicadores de tamaño del aislador, los contactos y otras partes para juzgar;
(3) Para evaluar la confiabilidad del tipo fijo y separado, se pueden probar la tolerancia de ensamblaje, el momento de resistencia, la fuerza de retención del pasador de conexión, la fuerza de inserción del pasador de conexión, la fuerza de retención en condiciones de estrés ambiental y otros indicadores del terminal y el conector.
Después de analizar los principales modos de falla y formas de falla del conector, se pueden tomar las siguientes medidas para mejorar la confiabilidad del diseño del conector:
(1) Seleccione el conector apropiado.
La selección de conectores no solo debe considerar el tipo y número de circuitos conectados, sino también facilitar la composición del equipo. Por ejemplo, los conectores circulares se ven menos afectados por factores climáticos y mecánicos que los rectangulares, presentan menor desgaste mecánico y se conectan de forma fiable a los extremos del cable, por lo que se recomienda elegir conectores circulares siempre que sea posible.
(2) Cuanto mayor sea el número de contactos en un conector, menor será la fiabilidad del sistema. Por lo tanto, si el espacio y el peso lo permiten, intente elegir un conector con menos contactos.
(3) Al seleccionar un conector, se deben tener en cuenta las condiciones de trabajo del equipo.
Esto se debe a que la corriente de carga total y la corriente máxima de funcionamiento del conector suelen determinarse en función del calor permitido al operar en las condiciones de temperatura más altas del entorno. Para reducir la temperatura de funcionamiento del conector, deben considerarse sus condiciones de disipación de calor. Por ejemplo, se pueden usar contactos más alejados del centro del conector para conectar la fuente de alimentación, lo que favorece la disipación de calor.
(4) Impermeable y anticorrosión.
Si el conector se utiliza en un entorno con gases y líquidos corrosivos, para evitar la corrosión, se debe considerar la posibilidad de instalarlo horizontalmente desde un lateral. Si la instalación requiere verticalidad, se debe evitar que entre líquido en el conector a través de los cables. Generalmente, utilice conectores impermeables.
Puntos clave en el diseño de contactos de conectores de alto voltaje
La tecnología de conexión de contacto examina principalmente el área de contacto y la fuerza de contacto, incluida la conexión de contacto entre terminales y cables, y la conexión de contacto entre terminales.
La confiabilidad de los contactos es un factor importante para determinar la confiabilidad del sistema y también es una parte importante de todo el conjunto del arnés de cableado de alto voltaje.Debido al duro entorno de trabajo de algunos terminales, cables y conectores, la conexión entre terminales y cables, y la conexión entre terminales y terminales, es propensa a diversas fallas, como corrosión, envejecimiento y aflojamiento por vibración.
Dado que las fallas del arnés de cableado eléctrico causadas por daños, holgura, caída y falla de los contactos representan más del 50% de las fallas en todo el sistema eléctrico, se debe prestar total atención al diseño de confiabilidad de los contactos en el diseño de confiabilidad del sistema eléctrico de alto voltaje del vehículo.
1. Conexión de contacto entre el terminal y el cable.
La conexión entre terminales y cables se realiza mediante engarce o soldadura ultrasónica. Actualmente, el engarce y la soldadura ultrasónica se utilizan comúnmente en arneses de cables de alta tensión, cada uno con sus propias ventajas y desventajas.
(1) Proceso de engarce
El principio del proceso de crimpado consiste en utilizar fuerza externa para presionar físicamente el cable conductor en la parte crimpada del terminal. La altura, el ancho, la sección transversal y la fuerza de tracción durante el crimpado son factores clave para la calidad del crimpado, que determinan su calidad.
Sin embargo, cabe destacar que la microestructura de cualquier superficie sólida finamente procesada siempre es rugosa e irregular. Tras el engarce de los terminales y cables, el contacto no se produce en toda la superficie de contacto, sino en algunos puntos dispersos en ella. Por lo tanto, la superficie de contacto real debe ser menor que la teórica, lo que explica también la alta resistencia de contacto del proceso de engarce.
El engarce mecánico se ve muy afectado por el proceso de engarce, como la presión, la altura de engarce, etc. El control de la producción debe realizarse mediante métodos como la altura de engarce y el análisis de perfil/metalográfico. Por lo tanto, la consistencia del engarce es media, el desgaste de la herramienta es alto y la fiabilidad media.
El proceso de crimpado mecánico es un proceso consolidado y con una amplia gama de aplicaciones prácticas. Es un proceso tradicional. Casi todos los grandes proveedores ofrecen productos para arneses de cables que utilizan este proceso.
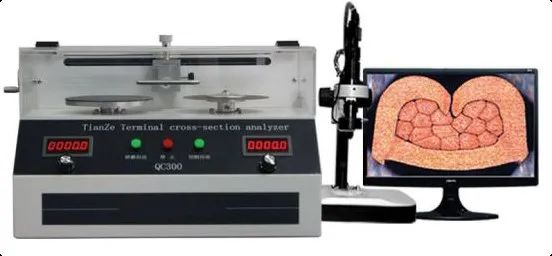
Perfiles de contacto de terminales y cables mediante proceso de crimpado
(2) Proceso de soldadura ultrasónica
La soldadura ultrasónica utiliza ondas de vibración de alta frecuencia para transmitirse a las superficies de dos objetos a soldar. Bajo presión, las superficies de ambos objetos rozan entre sí, formando la fusión entre las capas moleculares.
La soldadura ultrasónica utiliza un generador ultrasónico para convertir la corriente de 50/60 Hz en energía eléctrica de 15, 20, 30 o 40 kHz. Esta energía eléctrica de alta frecuencia se transforma en movimiento mecánico de la misma frecuencia a través del transductor, el cual se transmite al cabezal de soldadura mediante un conjunto de dispositivos de bocina que pueden variar su amplitud. El cabezal de soldadura transmite la energía de vibración recibida a la unión de la pieza a soldar. En esta zona, la energía de vibración se convierte en energía térmica mediante fricción, fundiendo el metal.
En términos de rendimiento, el proceso de soldadura ultrasónica tiene una pequeña resistencia de contacto y un bajo calentamiento por sobrecorriente durante mucho tiempo; en términos de seguridad, es confiable y no es fácil de aflojar y caer bajo vibraciones a largo plazo; se puede utilizar para soldar entre diferentes materiales; se ve afectado por la oxidación o el recubrimiento de la superficie. A continuación; la calidad de la soldadura se puede juzgar monitoreando las formas de onda relevantes del proceso de engarce.
Aunque el costo del equipo del proceso de soldadura ultrasónica es relativamente alto y las piezas metálicas a soldar no pueden ser demasiado gruesas (generalmente ≤5 mm), la soldadura ultrasónica es un proceso mecánico y no fluye corriente durante todo el proceso de soldadura, por lo que no hay Los problemas de conducción de calor y resistividad son las tendencias futuras de la soldadura de mazos de cables de alto voltaje.
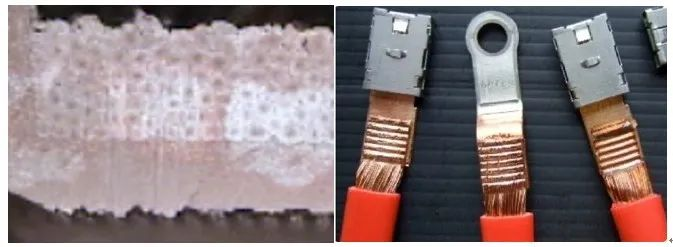
Terminales y conductores con soldadura ultrasónica y sus secciones de contacto
Independientemente del proceso de crimpado o soldadura ultrasónica, una vez conectado el terminal al cable, su fuerza de extracción debe cumplir con los requisitos estándar. Una vez conectado el cable al conector, la fuerza de extracción no debe ser inferior a la mínima.
Hora de publicación: 06-dic-2023